Визит на производство ООО «Протех»
Компания «Протех» была создана в 2007 году как дистрибьютор оборудования для производства электроники, но уже много лет занимается также разработкой и производством собственных технологических установок. Мы побывали на новой площадке ООО «Протех», а точнее – его дочерней компании НПП Протон, где производятся ванны ультразвуковой (УЗ) отмывки, планетарные миксеры для смешивания материалов, а также установки струйной отмывки с вакуумированием, которые, как нам рассказали представители компании, не имеют аналогов в мире.
Недавно «Протех» взялся за крупный проект, также уникальный не только для нашей страны, но и для всего мира, – разработку комплекса оборудования для изготовления жгутов. Данный комплекс будет автоматически выполнять все операции, начиная от подготовки проводов и заканчивая раскладкой и вязкой жгутов, так что монтажникам останется только распаять зачищенные концы проводов в разъемах. В рамках нашего визита на предприятие его представители продемонстрировали в том числе элементы данного комплекса.
Новая производственная площадка: как она появилась
Как нам рассказали главный инженер проекта ООО «Протех» Алексей Горбач и руководитель отдела маркетинга компании Юлия Коваль, то, что иностранные компании не могут полностью закрыть потребности российских производителей, стало понятно еще тогда, когда компания занималась исключительно дистрибуцией зарубежного оборудования. Поэтому приходилось выбирать решения, наиболее близкие к тому, что было нужно, и адаптировать их под задачи конкретных заказчиков. «Когда мы стали разбираться в оборудовании более глубоко, мы поняли, что зарубежные поставщики продают нам оборудование втридорога, если не больше. В нашей стране есть талантливые инженеры, конструкторы. Еще со времен Советского Союза у нас осталось много людей, пусть и в возрасте, которые прекрасно разбираются в этих областях; выросло и новое поколение высококлассных специалистов. Поэтому логично, что в рамках развития „Протеха“ мы пришли к созданию собственного производства, которое сосуществует с направлением продаж в рамках нашей компании», – сказал Алексей Горбач. «С 2014 года, когда был объявлен курс на импортозамещение, мы стали понимать, что наш внутренний рынок растет, что растет спрос именно на оборудование, производимое в России, – добавила Юлия Коваль. – Первым продуктом, который мы импортозаместили еще до появления своей производственной площадки, стали дымоуловители Duet. Мы по-прежнему изготавливаем их у своего партнера, компании „Вельтпласт“. Наше же собственное производство началось с УЗ-ванн».
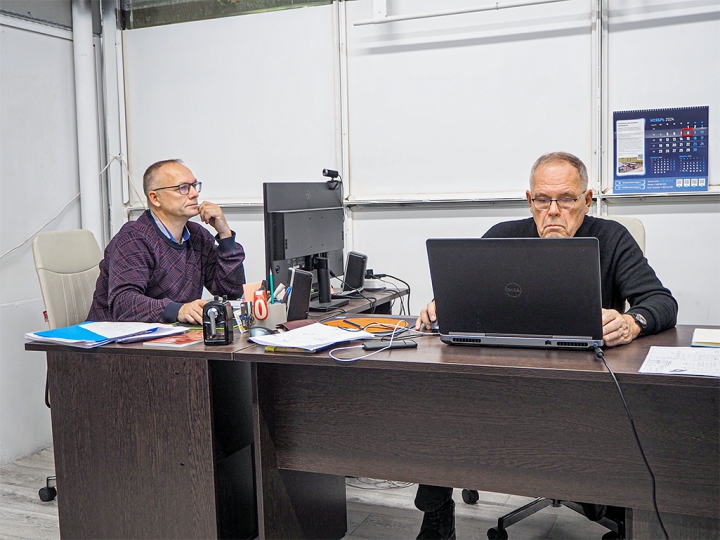
Изначально компания снимала небольшое помещение для производственных нужд. Но спрос на продукцию рос, и в определенный момент встал вопрос о создании новой площадки, более просторной и удобной. Однако найти помещение для нее оказалось непросто. «Мы обзвонили все технопарки Москвы, но не нашли там места. Это при том, что мы делаем уникальные продукты, которые кроме нас сейчас в России никто не делает», – рассказал Алексей Горбач.
В результате удалось найти площадку, занимающую часть промышленного помещения, которое было построено еще в советское время. В нем был пожар, после чего оно, фактически, находилось в запустении и использовалось как склад металлолома. Компании пришлось за свой счет приводить это помещение в порядок.
При этом площадка оказалась удобной для организации производства. «В Советском Союзе многие вещи были хорошо продуманы. Так, часто административные подразделения, конструкторский и технологический отделы располагали на антресолях над производственной площадкой. Это позволяло „сократить расстояние“ от этих подразделений до цехов, чтобы они не были оторваны от производственной жизни, – отметил Алексей Горбач. – Такие антресоли сохранились здесь, чем мы воспользовались, разместив здесь соответствующие подразделения».
Еще одна деталь – восстановленные стенды на входе на производство, на которых расположены наглядные инструкции по технике безопасности и другая полезная информация.
По словам представителей компании, новая площадка значительно больше той, что была у предприятия ранее, однако и ее уже становится мало. «В этом здании мы арендуем еще и подвальное помещение площадью 158 м2, начинаем размещать там оборудование, будем запускать новые линии», – рассказал нам Алексей Горбач.
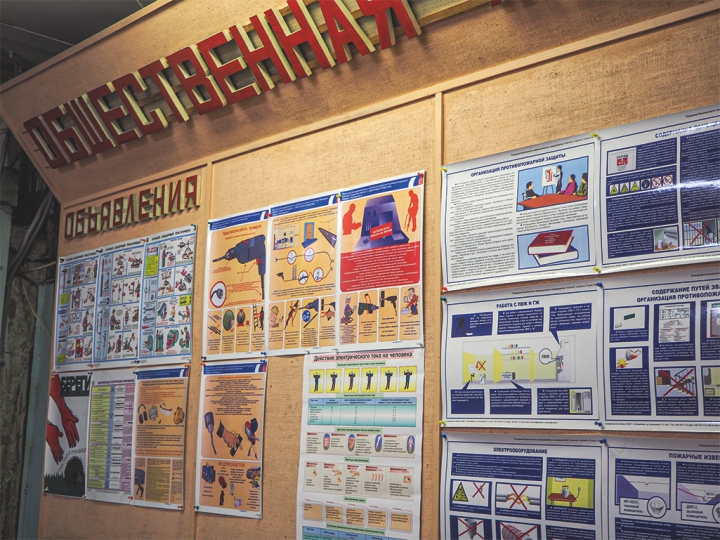
Производство ванн уз-отмывки
На первом участке, который нам показали представители предприятия, производятся ванны УЗ-отмывки под торговой маркой ХимСоник. Компания выполняет полный цикл проектирования, изготовления и настройки данного оборудования. «Мы выпускаем ванны различного объема – примерно от 0,5 л и до 2,5 тыс. л, – рассказал Алексей Горбач. – Несколько дней назад мы как раз отгрузили одну очень крупную ванну с подъемником для массивных отмываемых изделий. Подъемник мы также разработали сами, на основе лебедок и тросов. Обычно такие подъемники очень дорогие, но нам удалось создать весьма экономичное решение. Сейчас в России, кроме нас, есть только одна компания, способная делать такие крупные ванны УЗ-отмывки».
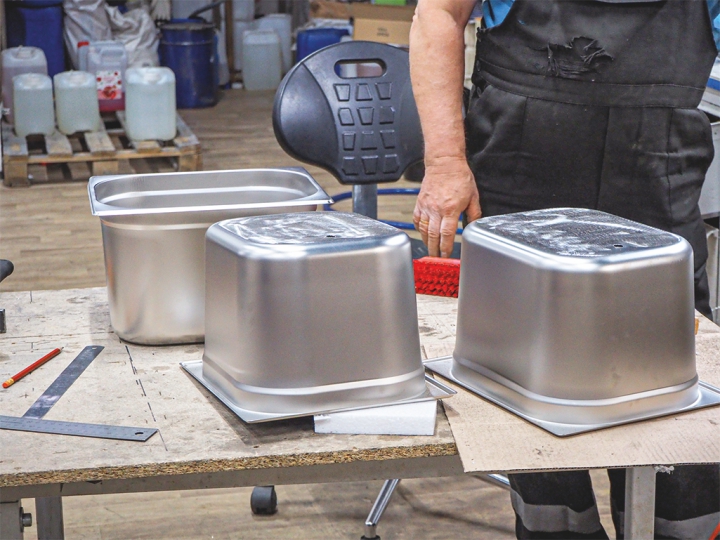
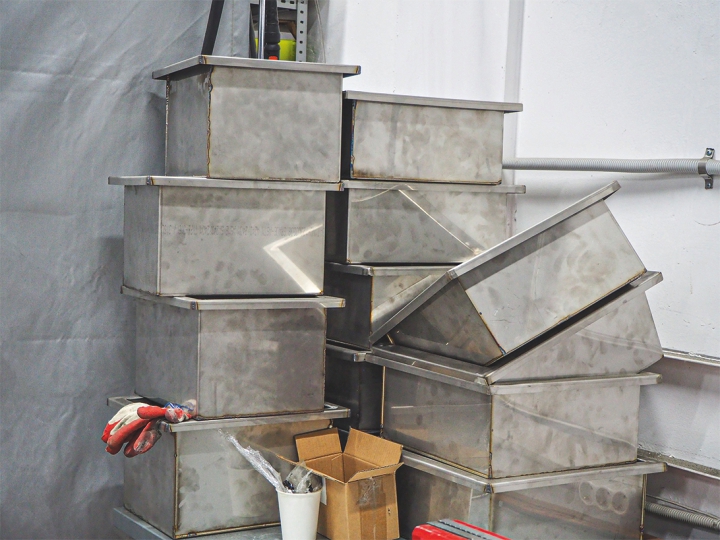
Учитывая, что ванны УЗ-отмывки выпускаются предприятием серийно, мы поинтересовались у представителей компании, как удается конкурировать с азиатскими решениями в данной сфере, а также не образуется ли конкуренция между собственной продукцией ООО «Протех» и той, которую компания поставляет в качестве дистрибьютора.
На наш вопрос ответила Юлия Коваль: «У нас нет никакой внутренней конкуренции. То, что мы поставляем как дистрибьютор – это готовые серийные решения, вы-пускаемые в больших количествах. В них тем или иным образом изменить технические характеристики, размеры и т. п. не представляется возможным. А на производстве такая возможность есть. Поэтому, вообще говоря, мы производим уникальные изделия под конкретные задачи. Более того, здесь есть некоторая синергия: там, где мы можем взять готовое решение, мы берем готовое, а где не можем – создаем нужное решение сами. Например, если нам нужно дополнить комплект нашего оборудования неким аксессуаром, таким как шприц для дозатора, конечно, нам проще и дешевле купить его у производителя, выпускающего эти шприцы миллионами штук, чем изготавливать собственную пресс-форму и отливать шприц самостоятельно».
Алексей Горбач добавил: «Если говорить об УЗ-оборудовании, у нас действительно налажено его серийное производство. Наша компания выпускает несколько серий стандартных УЗ-ванн, решающих различные задачи. Также мы выполняем индивидуальные проекты под конкретные требования заказчиков. УЗ-ванны, которые производятся в Азии, дешевле наших, и мы их также предлагаем для, скажем так, „бытовых нужд“. Если бы дело было только в цене, нам было бы сложно с ними конкурировать. Но мы говорим о высокотехнологичном продукте, а дешевые азиатские решения – это сравнительно простой массовый продукт, подходящий для отмывки, например, медицинских инструментов, ювелирных изделий и т. п., но не печатных плат».
Если говорить о ваннах для повседневного применения (ХимСоник серий «Стандарт» и УН), чуть ли не единственным покупным элементом конструкции является, собственно, сама ванна – штампованная емкость. Впрочем, для случаев, когда ванны эксплуатируются в жестких условиях либо применяются для интенсивной работы, производитель предлагает серию «Профи» со сварной емкостью объемом до 56 л. Также с помощью сварки изготавливаются ванны больших и нестандартных размеров. «Сейчас наиболее распространенная в нашей отрасли сварка – аргонная. Мы также используем эту технологию. Но у нас есть еще и лазерная сварка, – сказал Алексей Горбач, показывая нам сварочный пост. – Я считаю, что за этой технологией будущее. Получаемые швы герметичные, практически не требуют обработки, а их качество гораздо выше, чем при аргонной сварке. И изделие меньше деформируется, поскольку меньший объем металла подвергается нагреву».
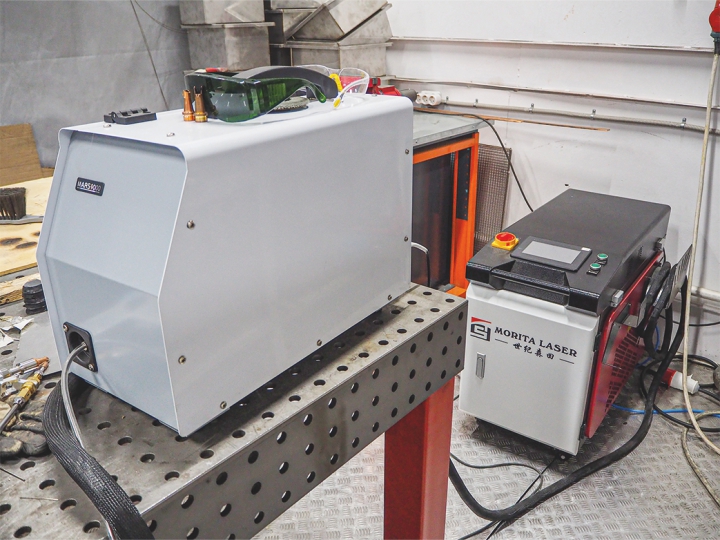
При изготовлении установок УЗ-отмывки к дну ванны с обратной стороны приклеиваются излучатели, формирующие ультразвуковые волны. Ультразвук приводит к кавитации (схлопыванию) пузырьков в жидкости. Именно процесс кавитации обеспечивает механическое разрушение и удаление загрязнений с обрабатываемых изделий.
Сборка УЗ-излучателей выполняется здесь же. Их крепление к ванне осуществляется на авиационный пленочный клей под определенным давлением. «Существует несколько способов монтажа излучателей, например на шпильку. Но каждый механический элемент влияет на эффективность работы излучателя на заданной частоте, – пояснил Алексей Горбач. – Эта эффективность зависит даже от момента затяжки винта, которым скрепляются части излучателя. Поэтому мы считаем приклейку оптимальным способом крепления излучателей к ванне. Мы смогли добиться очень высокого уровня надежности данного соединения, практически полностью исключающего возможность отклеивания».
На ванну в зависимости от ее размеров может устанавливаться разное количество излучателей. Как рассказали нам в компании, обычно каждая ванна предназначена для работы на одной частоте ультразвука. Сами излучатели могут работать на двух близких частотах, и иногда этот эффект используется для того, чтобы можно было обрабатывать изделия в двух режимах в одной ванне, однако это менее распространенный вариант. «Это похоже на стиральную машину с функцией сушки. Такие решения бывают, но если у вас есть возможность использовать для стирки стиральную машину, а для сушки – сушильную, этот вариант предпочтительнее», – объяснил главный инженер проекта.
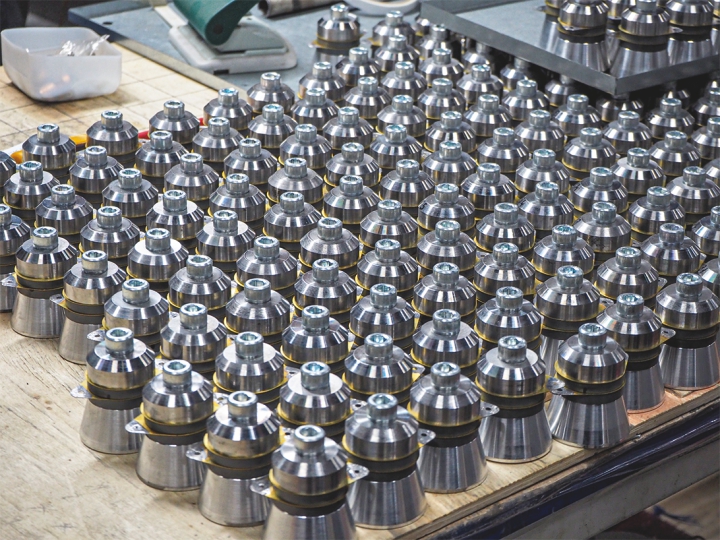
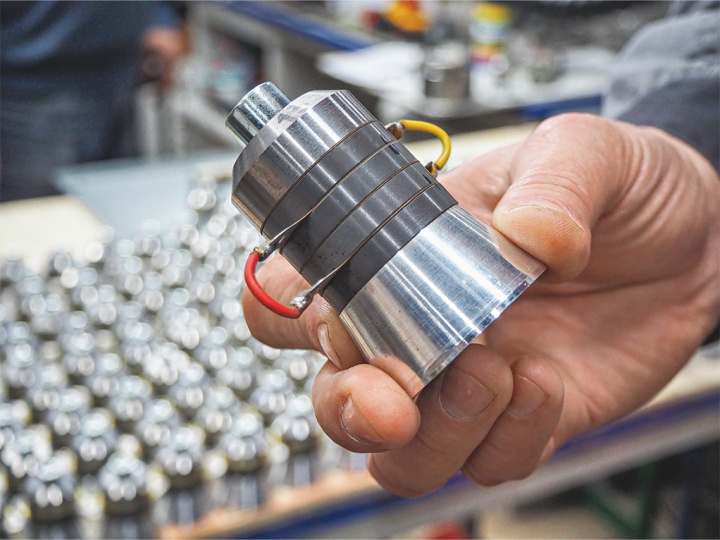
Отвечая на наш вопрос про выбор частоты ультразвука для конкретной задачи, он заметил, что, если речь идет о печатных платах, заказчик, как правило, хорошо знает, на каких режимах следует отмывать его изделия. Более того, некоторые электронные компоненты, например в стеклянных корпусах, можно повредить ультразвуком, и содержащие их платы могут отмываться только в струйных системах. Если же необходимо, допустим, снять окалину с некоторой металлической детали или удалить другое сложное загрязнение, то компания может провести необходимые исследования и предложить заказчику оптимальные режимы. Хотя для каждого конкретного изделия существует свой идеальный режим, можно выделить группы изделий, для которых будет хорошо подходить одна и та же частота и которые таким образом можно эффективно отмывать в одной ванне. «Обычно происходит так: для отмывки большинства изделий заказчика применяется одна ванна, и лишь несколько изделий либо отмываются вручную, либо в другой ванне – это зависит от финансовых возможностей и организации техпроцессов у заказчика», – отметил Алексей Горбач.
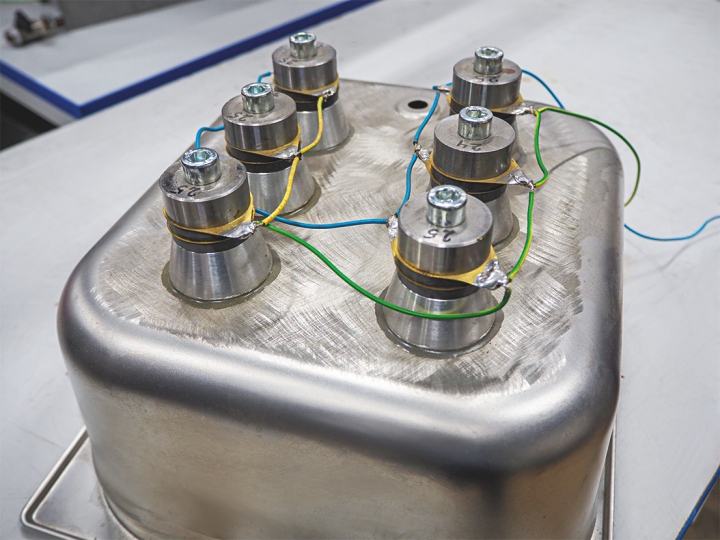
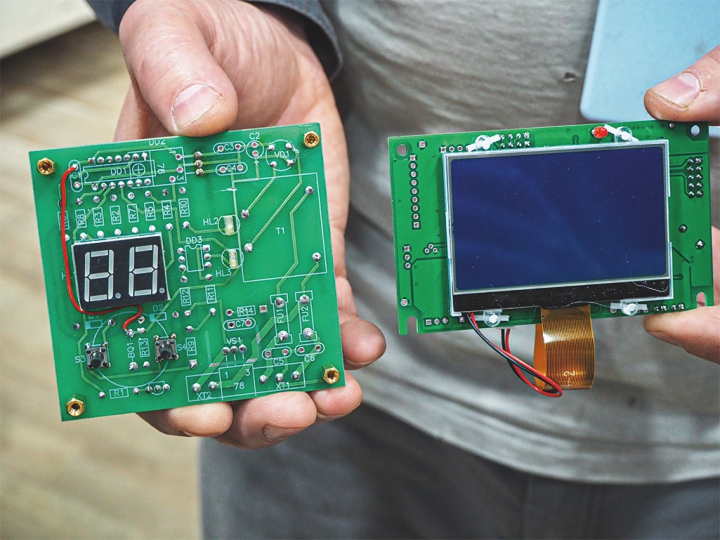
После того как УЗ-излучатели установлены и распаяны, собирается остальная часть установки. Корпусные детали изготавливаются компанией из металлических листов. Также в установку монтируется электронная схема управления, которая позволяет задавать режимы работы ванны – мощность излучения, температуру моющей жидкости и длительность цикла обработки. В ваннах УЗ-отмывки компании «Протех» применяются как аналоговые схемы управления, так и цифровые – более совершенные. Последние выполнены на основе микроконтроллера, управляющего ключами и аналоговыми каналами, и включают в себя ЖК-дисплей для отображения режимов и прочей информации. В цифровых ваннах также реализованы функции Sweep, Pulse и Degas, значительно повышающие качество отмывки. Цифровые схемы управления – покупные: их предприятие заказывает у своего партнера – НТФ «Техно-Альянс Электроникс», а программирование и настройка осуществляются уже самой компанией.
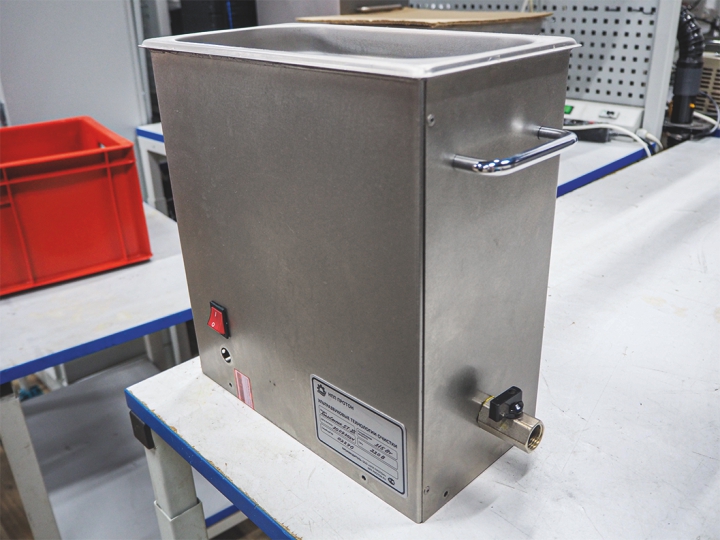
Оборудование струйной отмывки с вакуумированием
Установки струйной отмывки УСОТП-1 компании «Протех» – это уже единичные изделия. По крайней мере пока они не производятся серийно. Мы застали на производственной площадке предприятия вторую такую установку, которая находилась на стадии отладки. Первая система уже работает у одного из заказчиков компании.
По словам представителей предприятия, это оборудование не имеет аналогов в мире. Его главной особенностью является создание вакуума в камере отмывки – до 0,2 атм. Этим объясняется большая толщина стенок и дверцы камеры, которая составляет 6 мм.
«Конечно, это не глубокий вакуум, но такого разрежения хватает для того, чтобы извлекать пузырьки воздуха из-под компонентов, установленных на плату с малым зазором, из глухих отверстий и подобных мест», – рассказал Алексей Горбач. За счет вакуума обеспечивается проникновение отмывочной жидкости в малые полости изделия, что позволяет эффективно удалять из них загрязнения даже при применении сравнительно простых и дешевых средств отмывки. «Мы эту технологию внесли в отрасль. До нас ее не было, – добавил главный инженер проекта. – Эта установка позволяет отмывать печатные платы и микроузлы с использованием обычных водных материалов до такого состояния, которое на импортных аналогах достижимо только с применением спиртосодержащих смесей, фреонов и т. п.».
По его словам, сейчас многие отечественные разработчики отмывочных жидкостей пытаются создать дешевые аналоги дорогих импортных материалов, но этот путь ошибочный, потому что действительно эффективные и качественные жидкости содержат в своем составе дорогие компоненты; создать качественную жидкость из дешевых компонентов не получится. А дешевые зарубежные смеси, преимущественно азиатские, не обеспечивают высокого качества и повторяемости отмывки и подчас приводят к различного рода дефектам, например к образованию белого налета.
Компания «Протех» пошла другим путем, разработав технологию, которая позволяет качественно отмывать печатные платы с применением проверенной и недорогой отечественной жидкости. «Средство, которое применяется в нашей установке, производится российской компанией уже многие годы и стóит почти на порядок дешевле зарубежных жидкостей, применяемых для струйной отмывки печатных плат, – сказал Алексей Горбач. – На мой взгляд, в таких вещах самое важное – это то, что должна быть и своя команда, и желание найти в России то, что нужно. В нашей стране есть огромный потенциал и в людях, и в производстве».
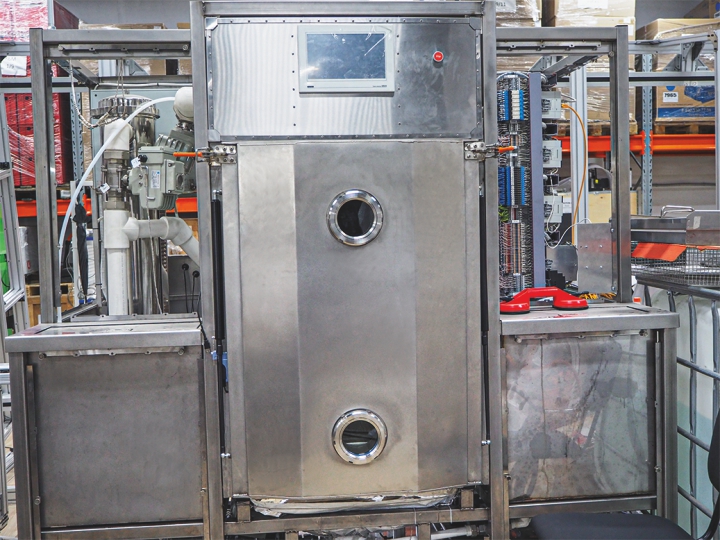
Так, фильтрация жидкости производится не только при сливе в бак по окончании цикла, но и постоянно в процессе ее циркуляции при отмывке изделия, что снижает вероятность его вторичного загрязнения. Для снижения сопротивления при прохождении жидкости был выбран фильтр с большой площадью. Тонкость очистки данной колонны составляет 0,5 мкм. Для прокачки жидкости через фильтр используется дополнительный насос. При этом данное решение оказалось достаточно дешевым. По словам Алексея Горбача, например, стоимость сменной части фильтра не превышает 1 тыс. руб.
Еще одна особенность данного оборудования заключается в том, как осуществляется сушка изделий после отмывки. После нагрева воздуха в камере до заданной температуры, порядка 115-130 °C, вновь выполняется вакуумирование, и в данном случае из малых полостей вытягивается уже оставшаяся в них жидкость. Кроме того, установка оборудована датчиком влажности от компании «Овен», что позволяет производить сушку не по времени, а до тех пор, пока изделия не будут действительно высушены. Алексей Горбач особо подчеркнул, что этот датчик внесен в Государственный реестр средств измерений.
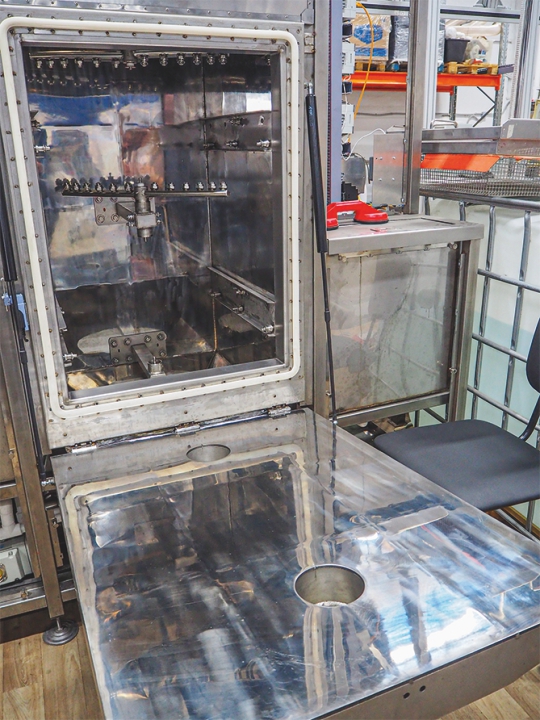
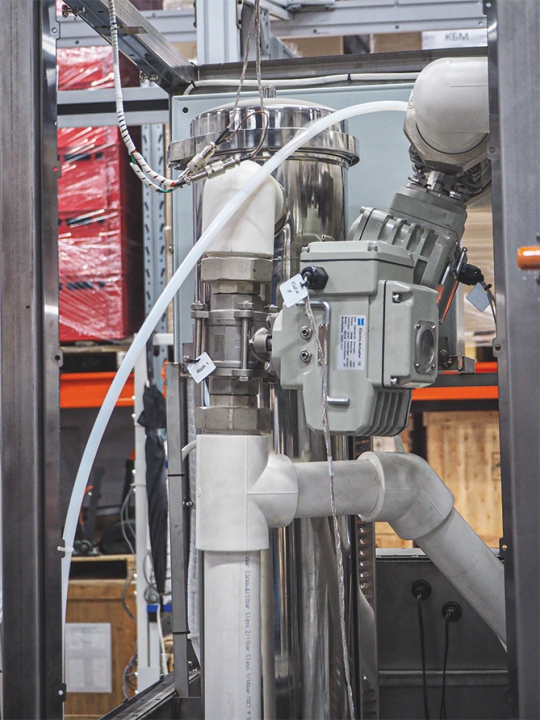
Также особенностью установки является применение одного ТЭНа для нагрева как отмывочной жидкости, так и воздуха в камере. Данный ТЭН был разработан специально по заказу компании «Протех». Это позволило уменьшить габариты оборудования.
Есть интересные решения и в программном обеспечении установки. В частности, по словам представителей компании, интерфейс управления выполнен так, что невозможно перейти к следующему шагу, если оператор, по мнению системы, что-то делает не так или не ознакомился со всеми предупреждениями и сообщениями. В этом случае кнопка «Пуск» просто не появляется на экране.
С особой гордостью Алексей Горбач показал нам шкаф управления установкой. «Шкаф разработан нашими инженерами на основе российских контроллеров „Овен“. Это действительно изделие очень высокого уровня. Мы его показывали на выставке, и у многих он вызывал большой интерес с точки зрения качества и проектирования, и монтажа».
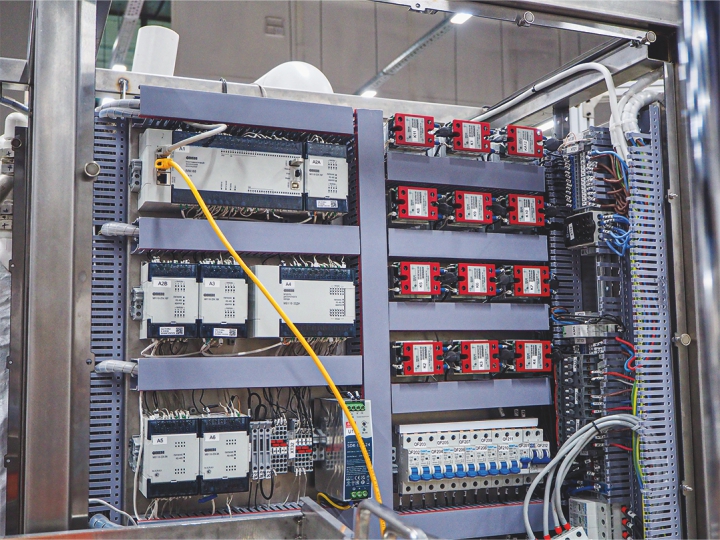
Планетарные миксеры
Компания «Протех» уже несколько лет поставляет миксеры для смешивания многокомпонентных материалов. Ранее это были установки производства ООО «Вельтпласт», о которых рассказывалось в нашем журнале ранее. Но некоторое время назад предприятием были разработаны собственные миксеры – Соло ВКС М – с улучшенной конструкцией, а их изготовление было локализовано на новой площадке НПП Протон.

Первое отличие новых установок заключается в увеличении количества перемешиваемого материала. Как нам рассказали в компании, если ранее поставляемые миксеры по заявленным характеристикам могли перемешивать до 750–800 г материала, то у новых моделей этот показатель выше более чем в два раза – до 2 кг. Необходимость в увеличении количества обрабатываемого материала была продиктована требованиями заказчиков.
«На новых миксерах мы достигли достаточно интересных результатов. Представьте: к 0,5 кг порошкового материала добавляется 20 мл красителя с пластификатором. Именно такую задачу мы решали на одном из предприятий – производителей бытовой химии. В миксере на оборотах, близких к максимальным, порошок плавится и превращается в однородную смесь равномерного цвета. Кстати, миксер мы создавали для военных, но у нас уже есть несколько проектов, где мы закрыли потребности чисто бытовой отрасли. Оказывается, есть проблема несовпадения результатов смешивания материалов на серийном производстве и в лабораториях. Как ни удивительно для нас было это слышать, на серийном производстве перемешивание, например вальцами, более качественное, чем могут добиться лаборатории этих же предприятий, что значительно усложняет разработку новых продуктов. Это уже следующий шаг после смешивания „Виксинта“, для чего эти миксеры создавались изначально, он требует значительно большей мощности и прочности оборудования», – рассказал Алексей Горбач.
Еще одним отличием новых миксеров является то, как устроена система вакуумирования емкостей при перемешивании материала: компрессор установлен не на вращающемся коромысле, а в неподвижной части миксера, что позволяет применять более мощный – промышленный – компрессор, так как его массогабаритные характеристики уже не имеют столь жестких ограничений, а конструкция в целом становится более надежной. Это удалось сделать благодаря специальной системе соединения компрессора с вакуумными трубками, закрепленными на коромысле, через которые осуществляется удаление воздуха из емкостей с материалом. Представители предприятия отметили, что данное решение уникально своей простотой и дешевизной, но раскрывать детали не стали – это ноу-хау, созданное двумя инженерами из Малоярославца – В. С. и В. В. Волковыми.
Система позволяет создавать в емкостях регулируемый вакуум до 0,1 атм при вращении коромысла со скоростью до 900 об./мин, а емкостей вокруг своей оси – до 800 об./мин.
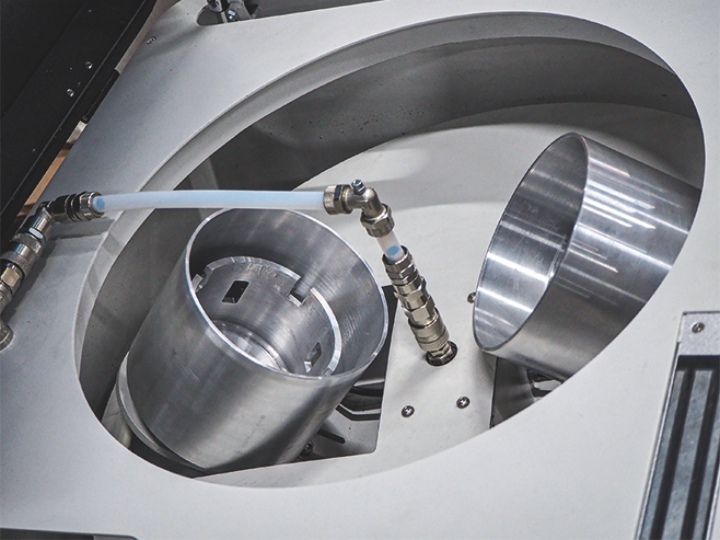
Все ключевые механические узлы, а также программное обеспечение миксера – собственной разработки компании «Протех». Однако корпус и бетонное основание, обеспечивающее устойчивость установки при перегрузках и вибрации, заимствуются у китайских миксеров – пока в России эти части сделать не удается. Сейчас компания находится в поиске соответствующих возможностей. Покупными являются и компоненты автоматики – драйверы, контроллеры, блоки питания, поскольку пока не удалось найти отечественных аналогов с нужной функциональностью, а также некоторые критичные элементы, от которых зависит надежность и безопасность оборудования, например фитинги вакуумной системы. Критические изделия – производства мировых лидеров, потому что только они обеспечивают необходимый уровень качества.
Также на производственной площадке размещена небольшая лаборатория, где сотрудники компании проводят различные исследования, в том числе выполняют подбор режимов смешивания для материалов заказчика. Алексей Горбач продемонстрировал примеры дефектов в отвержденных заливочных материалах, к которым приводит смешивание без вакуумирования и другие причины, например газация.
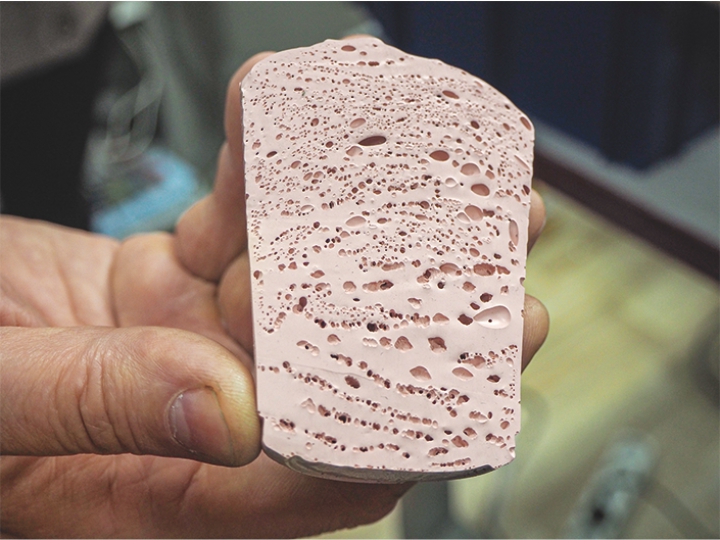
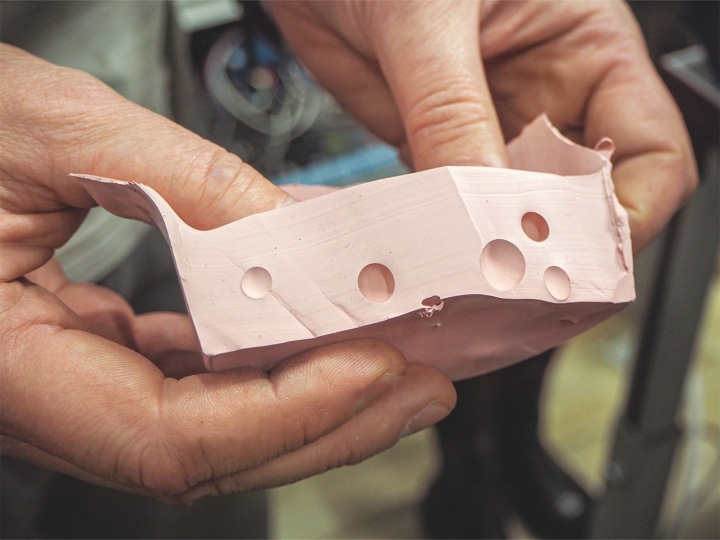
Для формирования комплексного решения подготовки и применения заливочных компаундов, клеев и подобных материалов миксеры компании «Протех» дополняются экструдерами и дозаторами производства НТФ «Техно-Альянс Электроникс», а также различными покупными аксессуарами. Такой комплект компания предлагает на рынке под названием Би-Микс.
Комплекс оборудования для автоматизации изготовления жгутов
В конце экскурсии по производственной площадке представители ООО «Протех» показали нам участок, на котором собирается и отлаживается оборудование для нового комплекса автоматизации изготовления жгутов. Этот проект выполняется по заказу одного из крупных российских предприятий, но в дальнейшем подобные комплексы могут быть внедрены и на других производствах, в особенности в тех отраслях, где создается сложное оборудование с большим количеством соединений, выполняемых с помощью жгутов, например в атомной промышленности.
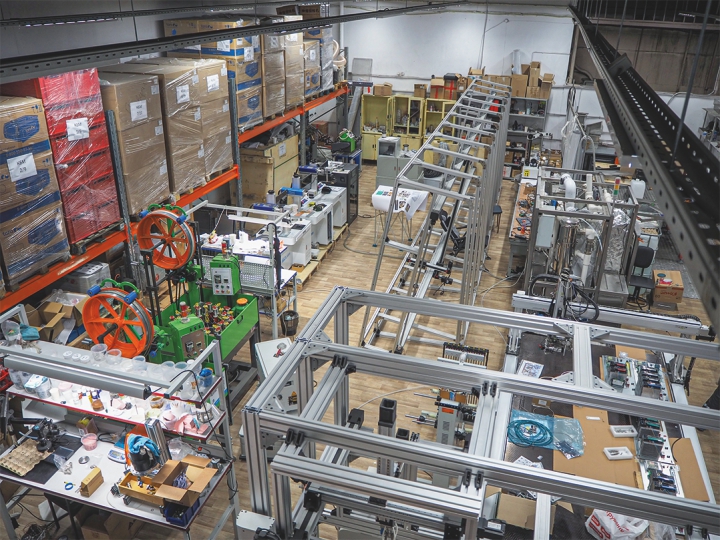
Как отметил Алексей Горбач, изготовление жгутов очень сложно автоматизируется, и это приводит к тому, что данная операция становится «бутылочным горлышком» всего маршрута создания электронной аппаратуры, в которой такие жгуты применяются. Кроме того, здесь велико влияние человеческого фактора: работник может ошибиться в том, какой провод должен быть припаян к определенному контакту разъема, а выявить такую ошибку очень сложно.
По словам главного инженера проекта, сейчас существует оборудование, которое позволяет автоматизировать только отдельные операции при изготовлении жгутов, но не весь процесс, включая раскладку проводов и вязку жгута. Попытки полной автоматизации предпринимались только в Японии, но в серию это решение не пошло.
Также были попытки использовать для раскладки проводов жгута робототехнические средства с применением двух рук KUKA с несколькими степенями свободы, но такие решения укладывали каждый провод за полтора десятка минут, что очень долго. Разрабатываемый комплекс позволит выполнять эту операцию примерно за 30 с. Таким образом, разрабатываемый комплекс станет уникальным решением, которое даст возможность значительно ускорить изготовление жгутов и свести к минимуму влияние человеческого фактора.
Комплекс включает ряд оборудования, часть из которого покупное, но основные компоненты разрабатываются самой компанией «Протех». Провода подаются с катушек по 8 шт. Пройдя предварительную подготовку: выпрямление, рихтовку, контроль и т. п., они поступают на станок с ЧПУ, где сматываются в небольшие бухты с помощью специального механизма с раскрывающимися лепестками. После того как на лепестки намотано необходимое количество провода, к нему подводится головка обрезки, провод обрезается, лепестки сводятся, и бухта провода падает на кассету, на которой дальше провод перемещается по программе по различным обрабатывающим станциям, где производится обработка концов провода.
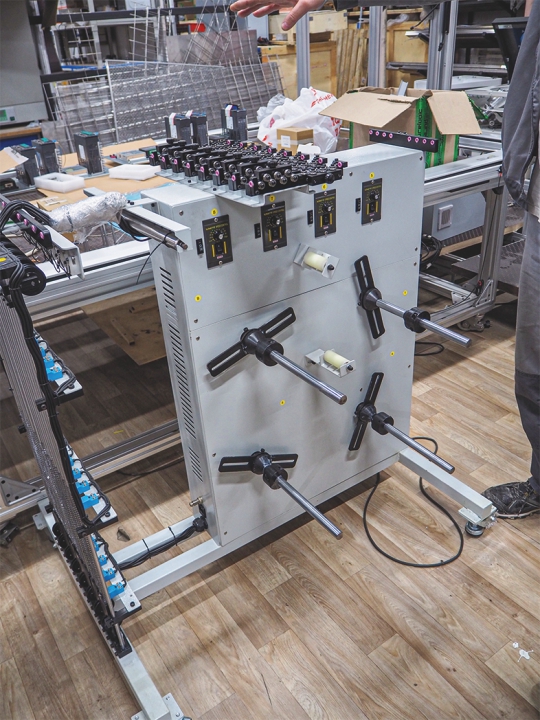
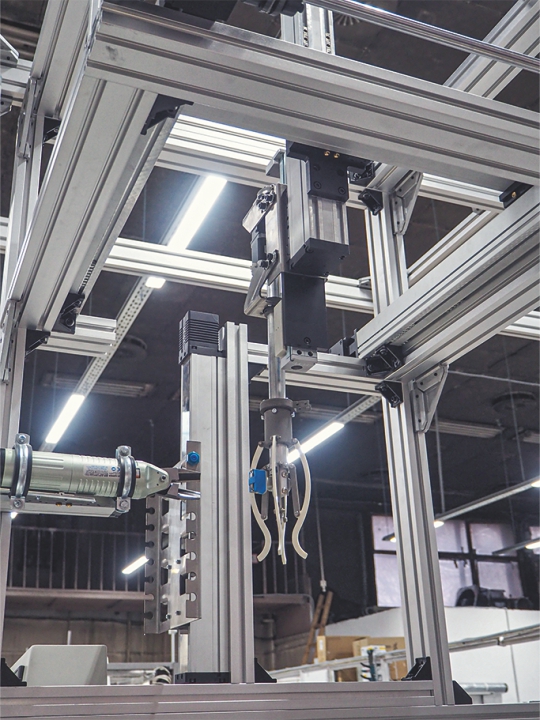
Для удаления изоляции используется лазер CO2. Этот лазер был приобретен в Китае, поскольку отечественный аналог, по словам представителей компании «Протех», оказался слишком дорогим. Однако для достижения требуемых характеристик китайская установка нуждалась в переработке. В ней были заменены панели управления и ПЛК, написано новое программное обеспечение. Обработанные провода поступают на следующий этап, где на большом координатном станке с ЧПУ (на данный момент его длина составляет 8 м) выполняется раскладка проводов жгута, а концы каждого провода продеваются в отверстия в картонных карточках, каждая из которых соответствует одному разъему. При этом на карточках нанесены обозначение разъема и номера его контактов, соответствующих каждому отверстию. Таким образом вероятность допустить ошибку при распайке проводов становится минимальной.
«Когда наша установка в присутствии заказчика разложила первый провод и закрепила его концы в нужных отверстиях картонных карточек, заказчик сразу понял, какую технологию мы ему предлагаем и какие возможности она открывает – рассказал Алексей Горбач. – Благодаря этому подходу мы сможем даже превысить показатели производительности, которые изначально закладывались в договоре, что очень кстати: у заказчика требования к объему производства выросли с момента подписания договора, и если бы мы формально выполнили наши обязательства, вероятно, ему производительности комплекса не хватило. Но мы, можно сказать, совершили „квантовый скачок“, пойдя по пути, который позволяет выполнять этот процесс даже быстрее, чем мы изначально ожидали».
Сам станок с ЧПУ, который сейчас дорабатывается, был приобретен в Китае. «Это уже вторая установка, с которой мы работаем. С первой мы ошиблись, она оказалась неподходящей. На самом деле, приобрести платформу ЧПУ не сложно, но мы выбирали ее с нуля, еще не зная всех тонкостей», – пояснил главный инженер проекта. Однако первая приобретенная платформа тоже пошла в дело. Сейчас она дорабатывается для перфорирования фанерных листов, из которых собирается поверхность для раскладки жгута. Оказалось, что заказ обработки таких листов на стороне слишком дорог, и в компании решили делать это своими силами.
Одним из ключевых элементов комплекса оборудования является головка, которая, собственно, осуществляет раскладку проводов. Именно благодаря ей удается достичь высокого уровня автоматизации и производительности выполнения данной операции. Алексей Горбач рассказал, что первый вариант головки разрабатывался почти год. Изначально ее конструкция получилась очень сложной. Затем инженеры компании стали оптимизировать ее, убирая всё лишнее. В результате получилась головка, которая сейчас установлена на станке, но это еще не окончательный ее вариант. «Когда головка была готова, мы просто запустили станок и стали наблюдать за его работой. И тогда мы увидели, что еще можно сделать, чтобы улучшить ее конструкцию и повысить надежность. Сейчас новая головка, в которой учтены эти моменты, уже почти готова, и скоро она заменит предыдущую версию в станке», – отметил он.
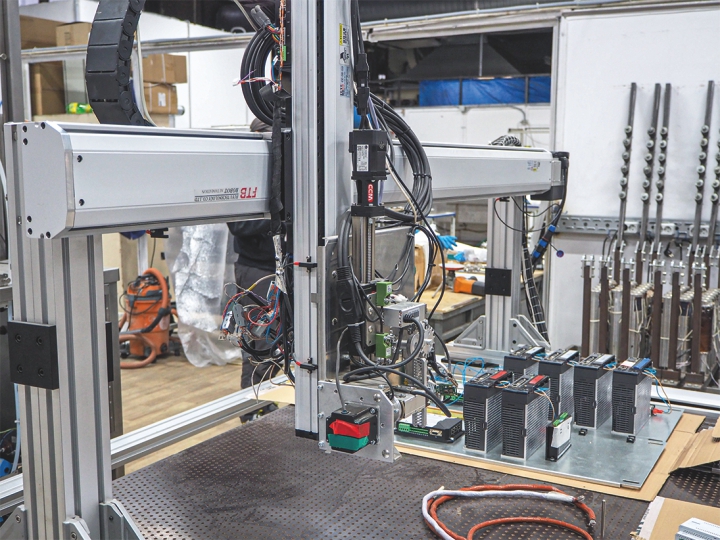
На головке также установлена камера технического зрения, осуществляющая инспекцию выполнения операции раскладки жгута, что позволяет не только контролировать процесс «на лету», но и готовить отчеты в рамках системы менеджмента качества. Программное обеспечение для системы технического зрения было также разработано специалистами компании «Протех».
***
Показывая покупные станки для комплекса оборудования изготовления жгутов, Алексей Горбач отметил, что все такие установки проходят отладку и на основе опыта работы с ними инженеры компании «Протех» составляют подробные инструкции. Эти инструкции затем входят в состав документации на типовой техпроцесс, который разрабатывается предприятием для любого создаваемого им оборудования. Такая документация составляется и для данного комплекса. Таким образом, «Протех» является не просто разработчиком и производителем оборудования, но поставщиком техпроцессов.
Приверженность компании данному подходу подтвердила и Юлия Коваль: «Наша компания – ответственный поставщик и производитель. Всегда, когда мы поставляем наше оборудование, наши специалисты выезжают к заказчику и отлаживают технологию, обучают персонал, показывают, как работать с этим оборудованием – именно в тех условиях, в которых находится заказчик. Поэтому наше оборудование не будет просто стоять в сторонке из-за того, что будет непонятно, как с ним работать, или окажется, что оно несовместимо с процессами заказчика, не подходит для его задач. Таких ситуаций у нас просто не бывает».
Ю. Ковалевский
Статья опубликована в журнале «Электроника: НТБ» №10 2024 г.